Quality control plays a pivotal role in the pharmaceutical industry, especially in the realm of Propaganda Cum Distribution (PCD) pharma manufacturing. With the primary goal of producing safe, effective, and high-quality pharmaceutical products, quality control processes are essential to safeguarding public health and maintaining industry standards.
This article explores the significance of quality control in PCD pharma manufacturing and its crucial role in ensuring the safety, efficacy, and regulatory compliance of pharmaceutical products. Ensuring adherence to stringent quality control measures is imperative for every PCD Pharma Franchise Company in India to uphold its reputation and provide reliable products to consumers.
Key Components of Quality Control in PCD Pharma Manufacturing
Quality control in PCD pharma manufacturing encompasses several key components, each contributing to the overall quality assurance process. These components include raw material testing, in-process monitoring, and finished product analysis.
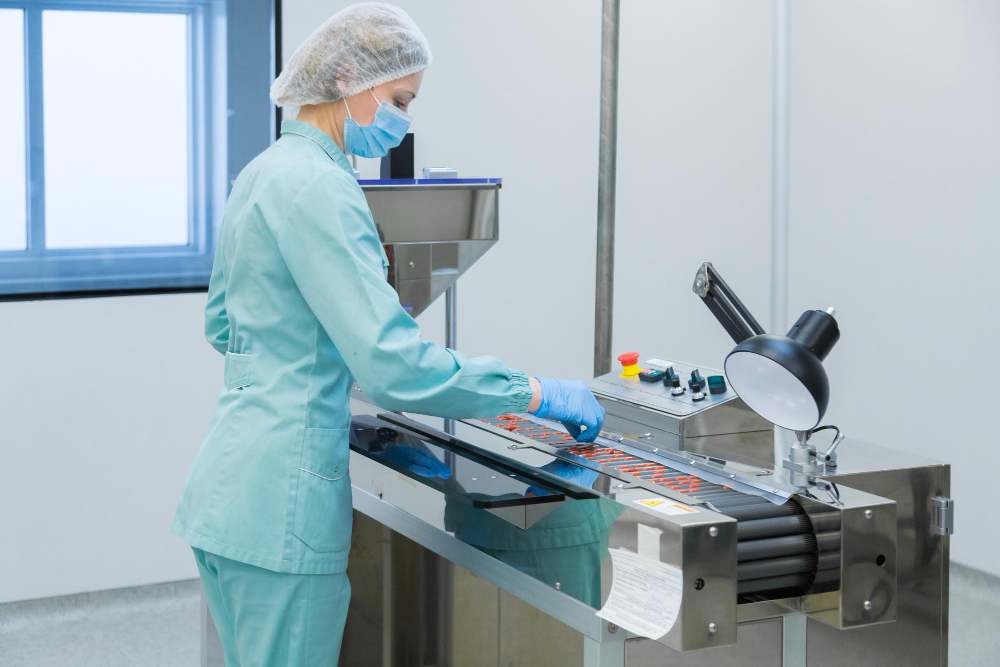
Importance of Raw Material Testing
Raw material testing is a fundamental aspect of quality control in PCD pharma manufacturing. Before production begins, pharmaceutical companies rigorously test raw materials to ensure their identity, purity, and quality. This step is crucial in preventing contamination and ensuring that only high-quality materials are used in the manufacturing process. Various tests, such as spectroscopic analysis and chromatography, are conducted to verify the quality of raw materials.
Significance of In-Process Monitoring
In-process monitoring involves real-time monitoring of the manufacturing process to detect any deviations or abnormalities. By closely monitoring critical parameters such as temperature, pressure, and pH levels, manufacturers can maintain consistency and identify potential issues early on. This proactive approach allows for prompt corrective action, minimizing the risk of product defects and ensuring batch-to-batch consistency.
Ensuring Quality through Finished Product Analysis
Once the manufacturing process is complete, comprehensive tests are conducted on the finished pharmaceutical products. These tests assess various attributes, including potency, purity, and stability, to ensure that the products meet established quality standards. Analytical techniques such as high-performance liquid chromatography (HPLC) and mass spectrometry are commonly used to analyze finished products and verify their quality.
Regulatory Compliance and Quality Control
Regulatory agencies such as the Food and Drug Administration (FDA) and the World Health Organization (WHO) play a vital role in setting guidelines and standards for quality control in the pharmaceutical industry. Compliance with regulatory requirements is essential for PCD pharma manufacturers to ensure that their products meet safety, efficacy, and quality standards. Failure to comply with regulations can result in serious consequences, including product recalls and legal repercussions.
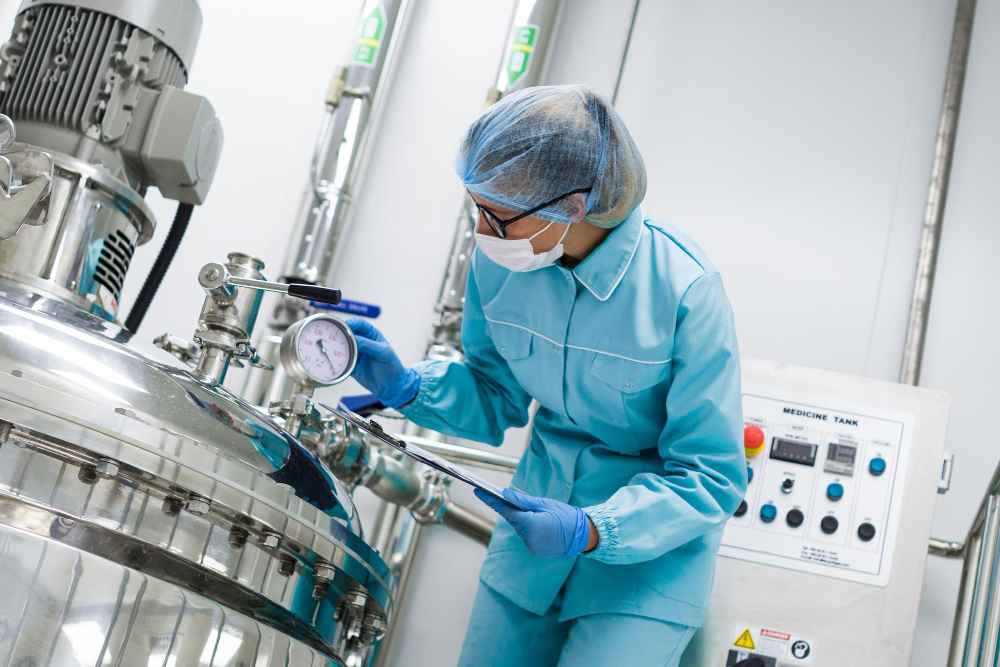
Continuous Improvement in Quality Control Practices
In today’s rapidly evolving pharmaceutical landscape, continuous improvement is essential to stay ahead of the curve. PCD pharma manufacturers must constantly evaluate and enhance their quality control practices to adapt to changing regulations and technological advancements. By investing in research and development, implementing advanced quality control technologies, and fostering a culture of quality within their organizations, manufacturers can ensure that their products consistently meet or exceed quality standards.
Quality control is the cornerstone of PCD pharma manufacturing, ensuring that pharmaceutical products are safe, effective, and of the highest quality. By implementing robust quality control processes, manufacturers can safeguard public health, maintain regulatory compliance, and build trust with consumers. As the pharmaceutical industry continues to evolve, quality control will remain a critical focus area, driving innovation and excellence in PCD pharma manufacturing.